
Duke University eNable
About Us

Duke University eNable is a student run organization that aims to connect amputees in the Durham area with 3D printed adaptive devices, free of cost. By conducting user-driven research and development projects, and by forging partnerships with prosthetics organizations both locally and globally, we hope to push the boundaries of 3D printed solutions to enable amputees with the devices we design and print.
Photo Gallery







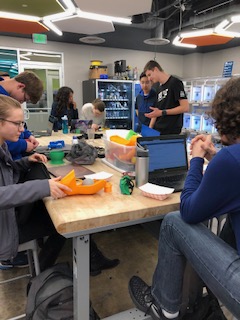
About Us
Duke University eNable is a student run organization that aims to connect amputees in the Durham area with 3D printed adaptive devices, free of cost.